Digital glass printing: UV vs ceramic inks
Share this blog:
In digital glass printing, 2 technologies reign supreme. Find out whether UV or ceramic inks come out on top.
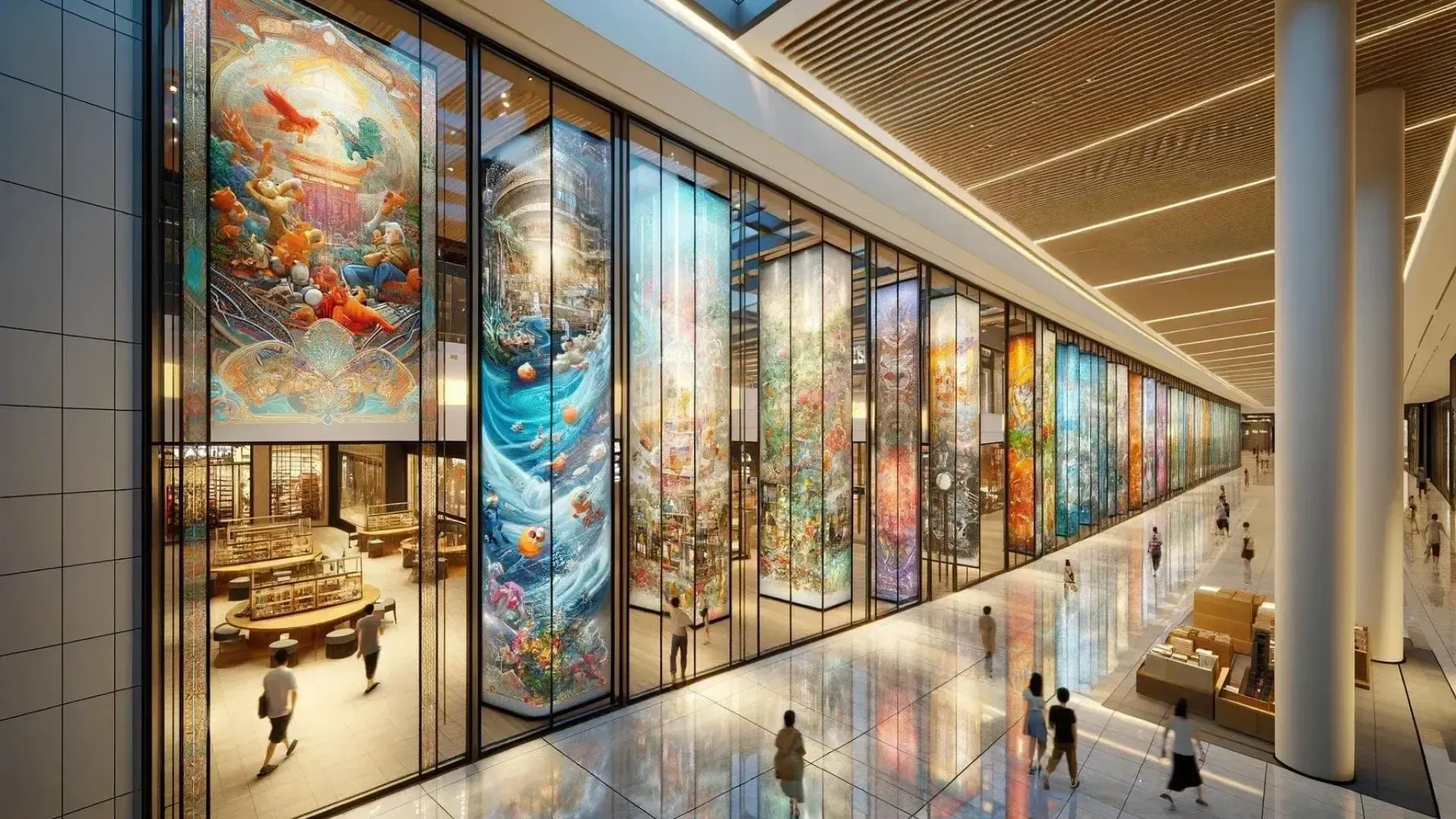
Have you seen what can be done with digital glass printing (DGP)? It's modern-day magic.
We're talking patterns, graphics and high-resolution photographs. We're talking huge buildings wrought from printed architectural glass – right down to colourful splashbacks and crisp, detailed glass wall art.
It's a new art form – one that architects, interior designers and other creative folk have embraced with open arms.
It wasn't always this way, though. Nowadays, if you can print something on paper, you can also print it on glass. But, believe it or not, the technology behind DGP only emerged in the 1990s – and took another 10 years or so to reach maturity.
The first method to hit the glass industry was ultraviolet pinning – a technique that uses UV-cured inks – followed in the late 2000s by ceramic printing.
Both technologies are widely available today. But which delivers the best results?
Full disclosure: here at ToughGlaze, we exclusively use heat-fired ceramic inks – for reasons that will soon become clear.
But we're going to give both techniques a fair shake and take an honest look at their pros, cons and printing performance.
UV glass printing
How it works
Printing on glass isn't easy.
Glass is a non-absorbent, non-porous material. Getting inks to stick to glass is like trying to mix oil and water. It won't happen without some sort of binder to help it stick and make delicious mayonnaise.
The glass industry first solved this problem with UV glass printing – also known as UV pinning.
UV pinning does what it says on the tin. It uses ultraviolet light to "pin" the inks to the glass so they stay firmly attached to its surface. In our mayonnaise analogy, it's the fresh egg yolk that makes the emulsion and keeps everything together.
The recipe requires four ingredients: a sheet of glass, a digital glass printer, a high-intensity UV light and a palette of special UV-cured inks.
These inks contain chemicals called photoinitiators. When the photoinitators are exposed to UV light, they cause the ink to dry instantly.
Incidentally, you can see this chemical reaction in action when you visit your local nail salon. Gel nail polish depends on photoinitiators to firm up and look fabulous.
On its introduction, the UV pinning process was nothing short of revolutionary. It allowed for detailed, vivid images to be printed onto slick sheets of glass – something that had confounded the industry for centuries prior.
Does it still live up to the hype? Let's find out.
Pros and cons
One of the chief benefits of UV glass printing is that it produces very vivid colours.
UV printing also allows for precise colour matching. With this method, what you see is what you get – the bright inks mean that digital images on a monitor can be recreated like-for-like on glass.
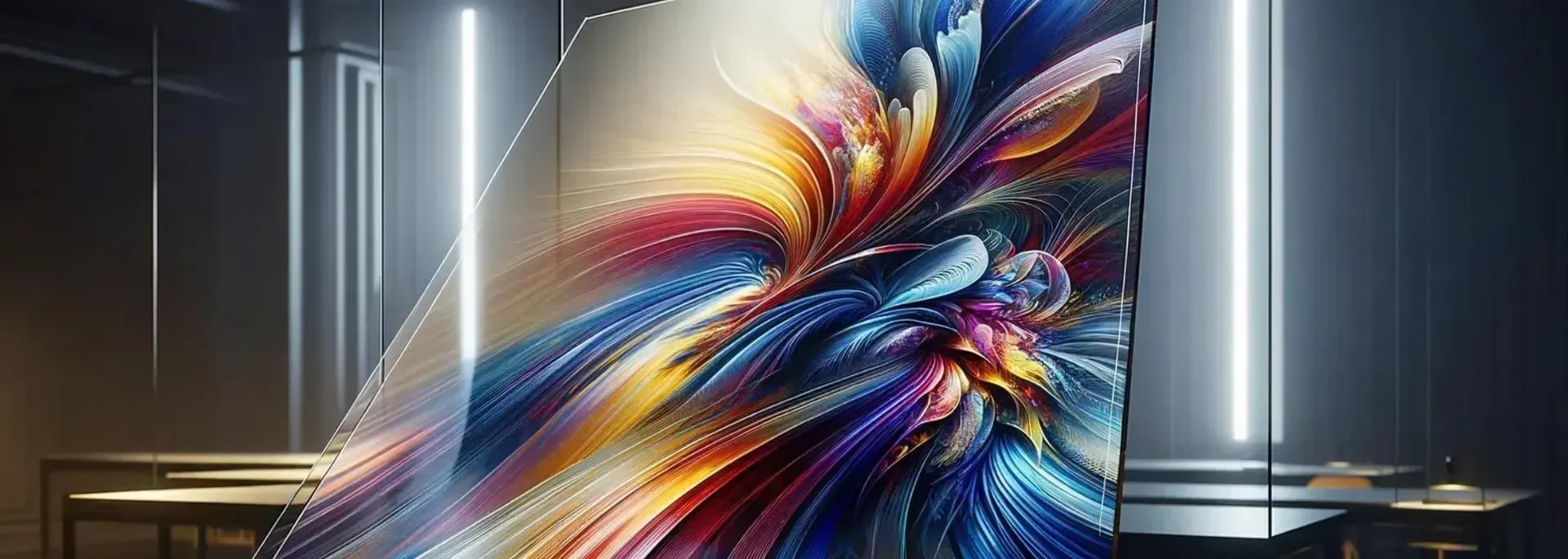
There are trade-offs, however.
The big one is durability. UV inks are resistant to UV rays – but only to a point. If you leave the glass in direct sunlight, you can expect the design to fade within five to 10 years.
And just as mayonnaise will separate if forgotten at the back of the fridge, so a UV-printed glass design will show its age unless you handle it with kid gloves. That ink is dried onto the glass, sure – but it
doesn't want to be. If you scratch or damage it, it won't hesitate to make a bid for freedom.
In practice, this means UV-printed glass is only really suitable for low-traffic indoor areas. Too much sunlight – or too much rough and tumble – will drastically shorten its lifespan.
Ceramic glass printing
How it works
There's a very important difference between UV and ceramic glass printing.
Both techniques bond inks to glass. But while UV printing creates a thin ink layer on top of the glass, its modern counterpart fuses heat-fired ceramic inks with the glass itself.
The process works because the inks contain microscopic particles of glass. It's this "ceramic frit" that gives the ink its name.
First, the design is applied to the glass using an industrial glass printer. Then the printed glass panel passes through a furnace. In simple terms, this "dries" the ink – but in chemical terms, something much more interesting happens.
Under the intense heat of the furnace, the ink solution evaporates, leaving behind only the ceramic frit and the pigment. For all intents and purposes, the frit, pigment and glass have become one. The ink is the glass and the glass is the ink.
Clever, eh?
Pros and cons
Ceramic inks are a whole lot stronger than UV-cured inks. We're talking Arnie in the 1980s versus a wet flannel from 1642.
UV-printed glass designs have a lifespan of five, 10 or maybe 15 years. But because they're fused with the glass, ceramic inks last for as long as the glass itself.
Seriously. The only way to destroy the design is to grab a hammer and start smashing.
This gives ceramic printing a huge advantage in terms of potential applications. Ceramic-printed designs are extremely resistant to UV and surface damage, so they can be used indoors or outdoors without worry. It's not uncommon to see ceramic inks decorating the exterior walls of glass buildings, for instance.
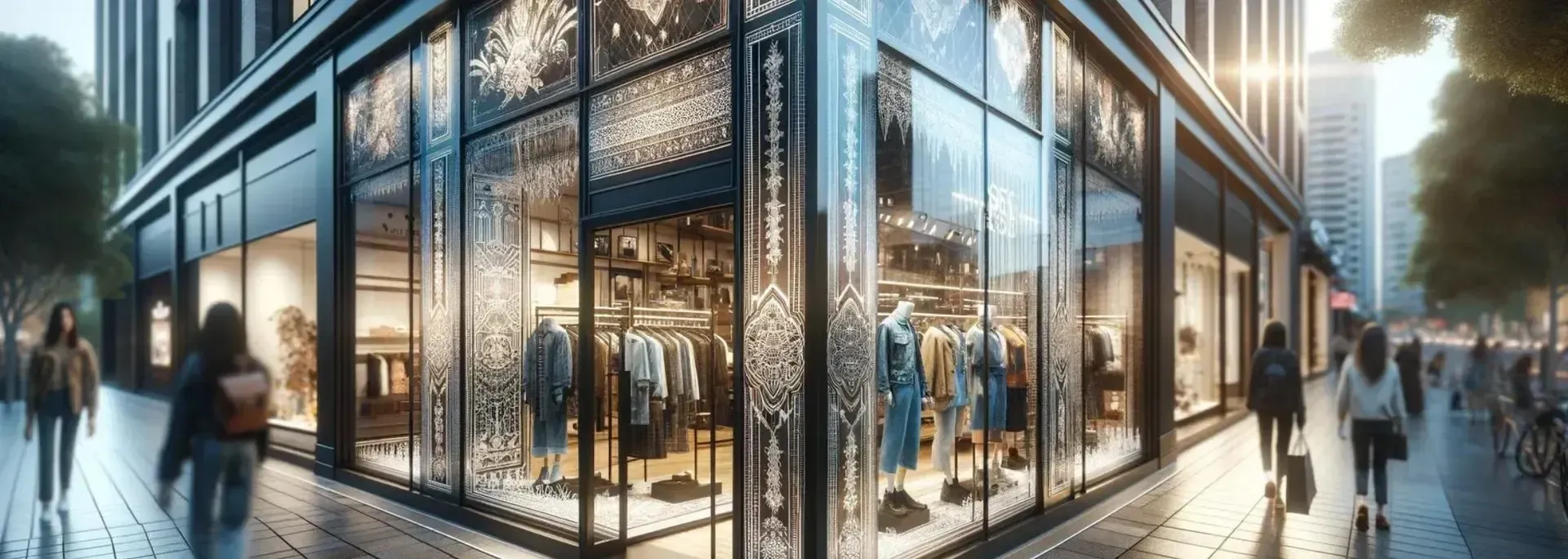
The only major downside – if you can call it that – is vividity. Ceramic inks are typically less bright and colourful than UV inks, though they do tend to produce clearer, stronger white tones.
We won't pretend this isn't a limitation. But it's one that digital printers have worked hard to overcome. Ceramic printing equipment is always used in conjunction with specialised software that's carefully tuned for the process.
With the right software and the right expertise, ceramic printing can reproduce digital imagery with little or no loss of colour.
Which is better?
UV and ceramic glass printing each have their pros and cons – but for most applications, ceramic comes out on top. There's a reason we use this method exclusively at ToughGlaze, after all.
Ceramic prints are robust, dependable and – thanks to the efforts of tech boffins – clear and vivid. They're especially suited for high-UV and high-traffic use cases, such as exterior glass walls. However, they're just as good for decorative glass panels and other interior applications.
UV printing is an older technology that comes with a longer list of caveats. The technology
might
just have the edge if you want a very vivid piece of glass wall art. But because of its UV sensitivity, it's only really suitable for interior projects.
Interested in
digital printing on glass? At ToughGlaze, we can print, cut and toughen glass – and our designs are guaranteed for the life of the glass itself.
Get in touch for a quick, honest quote.